Remote Peristaltic Pump Monitoring
Remote monitoring, increasingly seen in pharmaceutical processing operations, can be equally, if not more, beneficial for R&D departments tasked with fluid handling experiments or pilot testing. Applying remote monitoring to peristaltic pumps can positively impact departments who are tasked with fluid handling 24/7 but don’t have the staff to monitor the pumps. This opportunity to complete the R&D phase and move quickly through the pilot process can reduce the time to market for a new product and lower the cost of bringing a new product to market.
Remote Peristaltic Pump Monitoring through the IoT Increases Productivity and Reduces Costs in R&D and Pilot Plant Operations
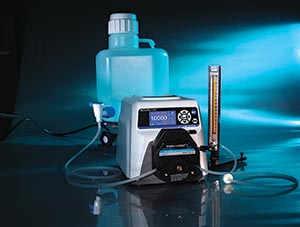
Today’s research and development is becoming more demanding. Companies need to find ways to increase their throughput without corresponding budget increases. At the same time, samples are more valuable than ever, so loss of a single batch can cost tens of thousands of dollars. R&D managers have been traditionally faced with two choices: leave their experiments running overnight unattended and risk loss of a valuable sample, or stop their work at the end of the day losing valuable productivity. Advances in remote monitoring through the Internet of things (IoT) have eliminated the need for a physical presence in fluid handling research and development, giving researchers the ability to remotely achieve much of the same monitoring they need in their workflow—whether that be preparation, fermentation, harvesting, or purification.
Conclusion
When operating with tight budgets or constrained resources, researchers can take advantage of new connectivity capabilities. Immediate benefits include an increase in productivity and a reduction in costs within their laboratory and pilot plant fluid handling operations. This connectivity can help improve time to market and allow unattended and overnight operation, while maintaining confidence that the process is being monitored.
Bluetooth connectivity allows for a hands-off approach providing flexibility of pump placement within the research process and can emulate the plant process thereby allowing a quicker time between the R&D lab to the process floor. This technology can also add a level of safety for employees by distancing then from harmful chemicals and biologics.
Cloud-based remote monitoring allows the researcher to track extended runs for a more seamless extension through pilot-scale and into full process. Read-only data transmission ensures data security—which is and should be a concern shared by researchers and product developers.
Masterflex® now offers new connectivity options on its most popular drives in L/S and I/P sizes to provide customers with maximum control over their pumping applications. In addition to Bluetooth and cloud-based monitoring, Masterflex’s new Advanced Communication drives support Ethernet/IP communications for automated processes. Learn more about remote pump monitoring plus Masterflex L/S & I/P Drives with Advanced Networking & Communication products on our website.