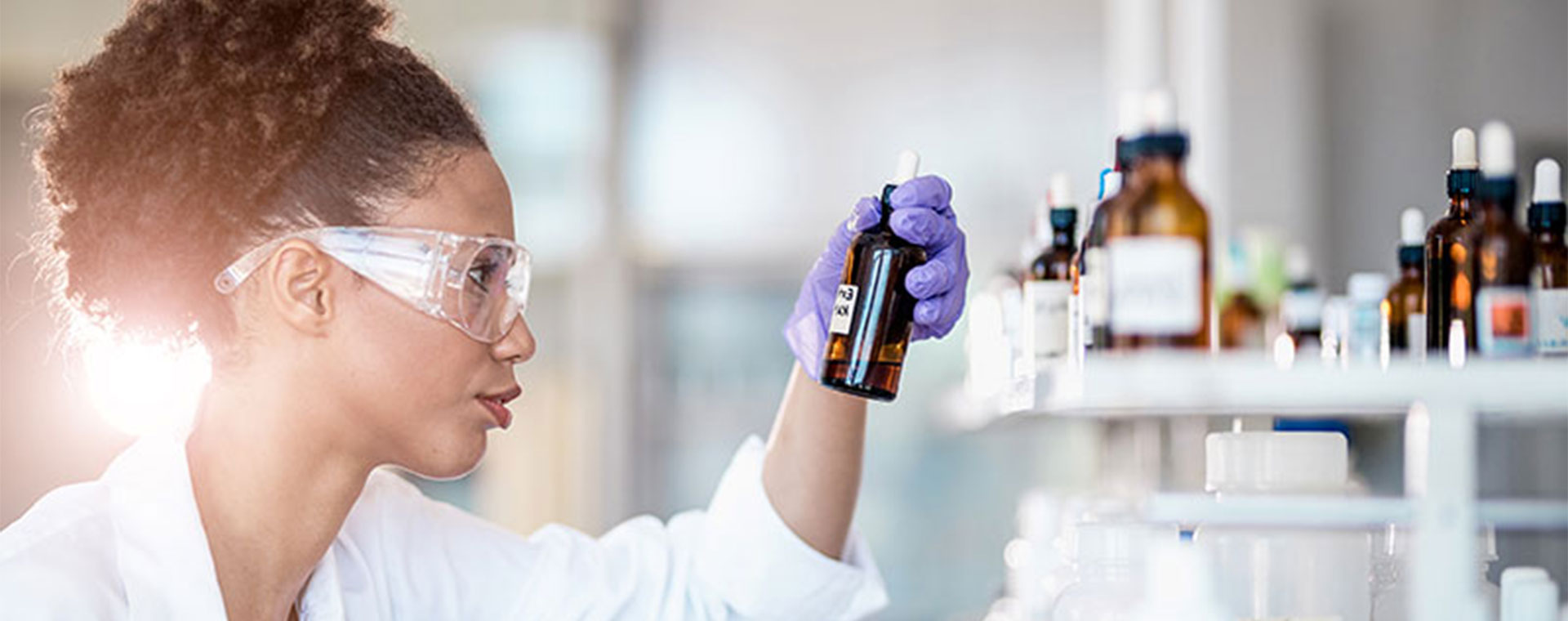
Avantor Services leverages its lab & production inventory management expertise to ensure a customer can continue the development of a potential treatment for COVID-19
Summary
In the wake of the global pandemic, altered supply chains, product availability, and staffing are just some of the challenges that life sciences companies are facing in supporting public health needs. As they rush to expand their diagnostic and production capabilities to address the COVID-19 pandemic, they are retooling how they are managing inventories.
Overview/Challenge
As one of our Biopharma customer’s prioritized and expanded their diagnostic tests and production of life-saving medicines to address the COVID-19 pandemic, they were faced with increasing challenges managing their inventory, including critical personal protective equipment (PPE).
In order to fast-track our customer’s development of diagnostic tests and production capabilities in developing a potential treatment, our Avantor team developed an inventory management solution to streamline the process of accurately allocating critical supplies across our customer’s network throughout the US. With more than 89 PPE items and over 100 hundred other items to manage and distribute, a robust solution to meet the increased demand was critical as their current inventory process was not designed for the needs of fast-tracking their development of COVID-19 diagnostic tests and potential COVID-19 treatment.
Action/Solution
Without the much-needed PPE, production plants would have been shut down. Working in collaboration with the customer, our onsite lab & production associates developed new inventory protocols and processes, enabling our customer to continue their important development of diagnostic tests and treatments for COVID-19.
Specific actions included:
- Developed new inventory protocols in collaboration with the customer to manage their PPE requirements across multiple sites from a centralized location
- Instituted an ordering process to coordinate between the customer’s procurement team and the Avantor distribution network to accurately forecast demand and timing of key items required to keep their diagnostic test production and treatment development running smoothly
- Established receiving protocols with the customer to ensure accuracy of asset allocation, inventory reconciliation and optimized internal logistics, such as matching incoming inventory to the order/allocation quantity and individual site requirements were accurately identified and processed
- Supported warehouse reconfiguration to optimize receipt of site-specific and bulk shipments, as well as improve tracking and tracing
- Established expediting process within the customer’s organization
- Created new tracking process with outside transportation companies to ensure timely shipments to the customer that enabled more effective planning and inventory allocation across sites
Results
As a result of our collaboration and instituting our new inventory management protocols, the customer has been able to continue with their development of diagnostic tests to identify COVID-19. These new protocols also ensured there were no interruptions in their development of a potential treatment for COVID-19. We have enabled the customer’s scientists to focus on what they do best, improving patient outcomes.