
Laboratory Compliance
Operational compliance with services tailored to meet your specific needs.
Avantor is your single point of contact to stay compliant with the evolving regulatory requirements reducing the risk of costly audit observations due to non-conformance.
Our large portfolio of service offerings ensures that all your equipment and instruments work within the defined parameters and meet the needs of your specific procedures.
Avantor offers the validation services you need for your laboratory. This includes:
- Installation qualification (IQ): Documents and verifies that environmental conditions for installation in your lab conform to the manufacturer’s guidelines and that the equipment is set up according to those specifications.
- Operational qualification (OQ): Shows how an instrument will function in your lab according to the operational specifications of the manufacturer. This step demonstrates and tests the equipment's control, functionality, and operation and if they meet the parameters provided by the manufacturer.
- Performance qualification (PQ): Tests and substantiates that the instruments and equipment consistently perform according to the criteria established for your laboratory. PQ is a documented verification of the equipment’s performance within the process and system throughout all anticipated operation ranges.
Operational Compliance with Avantor’s Single-Source Solution
Consolidating all your service needs with a single provider streamlines all compliance activities across all makes and models of your laboratory assets to a single source provider.
With our vast range of services, from temperature mapping to calibration, we aide our customers in obtaining all the qualification reports for regulatory compliance.
1.888.793.2300 or [email protected].
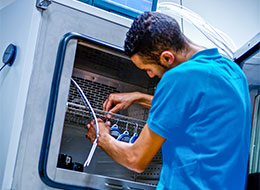
Equipment and instrument services
We validate your lab equipment, from installation to use
Equipment validation is a quality assurance process that documents that a piece of equipment meets manufacturer specifications and satisfies its requirements for accurate operation. We break the validation process into three steps—IQ, OQ, and PQ—to help ensure your lab complies with FDA, GMP/GLP, and other regulations.
Auditable records can ease compliance concerns
Successful audits require traceable, correct documentation of equipment calibration and services.
But the administrative tasks of documenting and organizing information about your equipment can be time-consuming and challenging, particularly if your lab has equipment from multiple vendors and manufacturers.
Just as calibration is necessary for reliable research results, maintaining documentation of calibration services is essential for audits. Many labs rely on their staff to calibrate and document the process, but that can be a problem unless trained in the calibration and documentation process.
Avantor’s trained and accredited technicians can help you plan for routine calibration and maintenance and ensure your documentation is organized and easily accessible whenever you need it, from when your new equipment is delivered until it is decommissioned and removed.
Find out how you can work with Avantor to help ensure your lab equipment is calibrated correctly, validated, and always in compliance. Contact us today.
Related content
Take a deeper dive into the value that our equipment management services provide.