A single provider – managing all aspects of equipment services from installation to decommissioning – helps create a fleet of equipment that is operational, available, and in compliance with internal and external regulations.
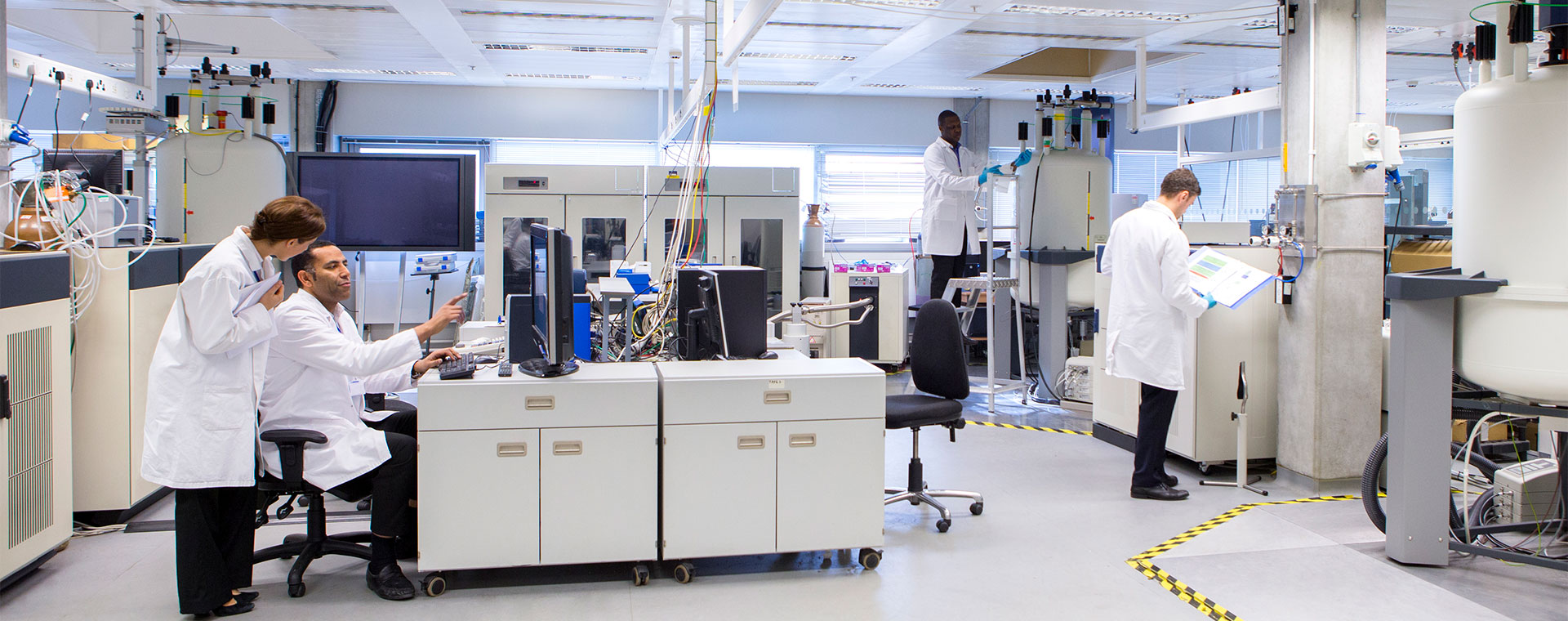
Equipment & Instrument Service Offerings
Avantor’s Equipment & Instrument Services (E&IS) is your one-stop, single-source solution for all your service needs. Our service solutions help support your workflows with improved productivity and enhanced operational efficiency, returning time to scientists to focus on science.
From installation to decommission, we partner with you to provide full life cycle support to meet your service needs.
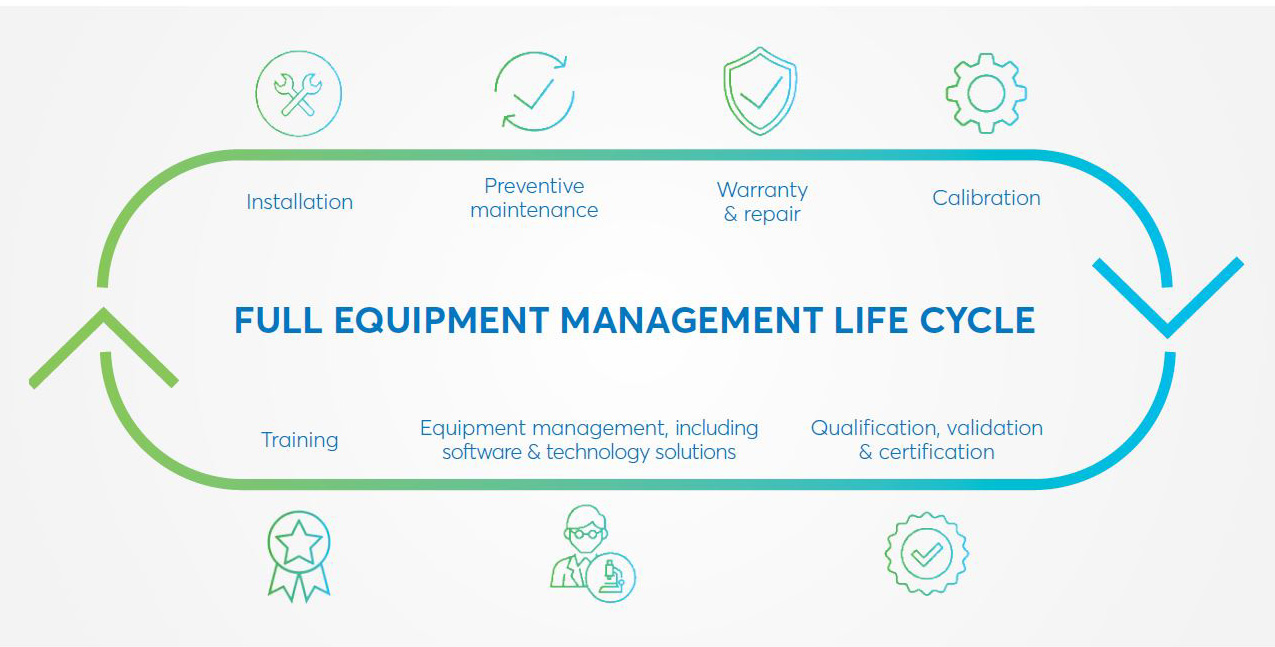
Avantor Equipment & Instrument Services (E&IS) Asset Consolidation
With the demand to innovate and deliver scientific solutions within tighter deadlines, it is crucial to increase laboratory productivity. Avantor’s one-stop, single-payor solution helps you overcome these barriers to success. Avantor’s Equipment & Instrument Services (E&IS) has the knowledge, experience, and expertise to help you stay in compliance and minimize your challenges of running your operations efficiently, allowing your scientists to focus on what they do best: science.
Avantor Equipment & Instrument Services (E&IS) Customized Service Solutions
Avantor provides end-to-end solutions for your facilities with customizable options to meet your needs. Our diverse portfolio of service partners and choices can create a customized solution for any of your organization’s projects.
The service levels and accreditations are fully customizable to meet all your compliance needs.
We can help you manage:
- Preventative Maintenance
- Calibration
- Repairs
- Service Contracts
- Decommission & Disposal
- And more...
Contact us at 1.888.793.2300 or [email protected]
Services
Installation, validation, calibration, preventative maintenance and service for all constant temperature unit makes and models.
Our service offerings include HPLC, UPLC, GC and mass spectrometer.
Certification and validation services for chemical fume hoods, laminar flow hoods and biosafety cabinets.
Service options to help you maintain the required accuracy of your laboratory instruments with calibration and PM service.
We offer direct traceability to NIST and compliance with all pertinent FDA, GLP/GMP, ISO, NCCLS, CAP, CLIA and 21 CFR requirements.
We offer weight calibration by ISO/IEC 17025, NVLAP-Accredited laboratories.
Equipment Management from Installation to Decommissioning – Optimized
Installation
We verify that the environmental conditions required for installation conform to the manufacturer’s guidelines and that the equipment is set up according to those specs.
Working with your team, we demonstrate how an instrument will function in the lab according to the operational specifications of the manufacturer, and test to make sure that it consistently performs according to the criteria you provide. Your scientists will be able to trust that equipment operates as intended.
Compliance
Working independently, or with a validated third party, our skilled technicians calibrate and validate your lab equipment and instruments against the manufacturer’s – and our own – specifications and standards. We also ensure they meet the local and national regulatory requirements (ISO, GMP/GLP, FDA etc.).
With our accreditation to the ISO 17025 standard in many countries, we are able to test and demonstrate that the equipment consistently performs according to the specified standards and criteria. Your team will have equipment that is precise so their research is accurate.
Maintenance
A routine approach to standard servicing, preventative maintenance, and routine calibrations keeps your equipment operating optimally. This, in turn, gives your scientists equipment that is both reliable and available – allowing them to depend on in-house instruments for their vital research.
Maintenance, as outlined in the manufacturer’s guidelines, will be completed on schedule so your teams can maintain their schedules.
Repairs
When a machine goes down mid-project, it is at best inconvenient and at worst a real crisis. Downtime is costly, both in money and in lost time for research.
Our skilled technicians, working with your in-house team or validated third-party service providers, respond quickly to repair requests. We are manufacturer agnostic and can help resolve problems with equipment ranging from pipettes to laminar flow cabinets.
To ensure we respond to your needs in a timely way, we track our reaction time from call to on-site service. Your team will know when to expect the equipment back online so they can get back to moving science forward.
Administration and Documentation – Simplified
In equipment management, digital solutions are key to driving efficiency up and spend down.
We’ll work with you to create an administrative flow, from procurement to decommission, that works for your teams. Using either existing systems or our proprietary software Equipment Manager, we ensure that invoices are fulfilled, calibration documentation is readily available, and service and maintenance requests are scheduled (and completed)!
By acting as your administrator we can:
- Track your vendors and suppliers and consolidate the list so it’s consistent across the ecosystem of your labs.
- Be a single point of contact for your equipment needs.
- Use the data we gather to identify problem areas in procurement, storage and use of equipment and address those pain points.
We also put clear Key Performance Indicators (KPIs) into place – such as time to repair and percentage of uptime and downtime – and use that data to make sure we are on track and meet, or even exceed, expectations.
A proactive approach to equipment management lets your teams plan ahead. They will know what equipment and supply resources are available, and when, and can trust that it’s operating as expected.